Set clear goals and metrics to track and, most importantly, don’t forget to seek employee feedback.
For manufacturing businesses, improving their operations is critical for their growth and success. Optimized manufacturing processes will directly impact your workplace performance, customer satisfaction, sales, inventory management, and so forth.
Therefore, if you have been struggling with poor manufacturing operations, here are five simple tips that may help you.
- Audit your Existing Workflow
If you have been in the industry for a while, it is time to review your existing workflow, see what changed, and identify your major pain points. Now, in the past, businesses had access to isolated data sets only. Today, with sophisticated tools based on artificial intelligence and machine learning, you can take a more granular approach to data analysis and understand the processes and conditions needed for improving workplace efficiency.
Here are a few simple steps to take when performing workflow audits:
- Make a list of goals for each task.
- Map out all workflows.
- Break workflows down into smaller tasks.
- Identify all roles and responsibilities.
- Test your equipment.
- Monitor workflows and ask for employee feedback.
- Detect the most common issues that need to be resolved.
- Remap your workflow.
- Automate Inventory Management
Inventory management is a critical aspect of your supply chain, as its purpose is to improve your inventory stock and prevent overproduction or overselling. By monitoring your stock levels, you will be able to understand the current market demand and optimize any part of your manufacturing process, from production to storage. This way, you will reduce costs, improve sales, and minimize inventory waste.
Now, while you were starting out, you probably used simple Excel spreadsheets to stay on top of your inventory. However, as your business grows, you will need to switch to automated inventory management tools. For example, when investing in MRP software, you will be able to streamline and centralize all business processes, from manufacturing, inventory management, and supply chain to sales and CRM.
- Take Advantage of Robotic Automation
The idea behind robotic process automation (RPA) is simple – you will use software to automate many manual and repetitive tasks. This way, your employees will finally have enough time to allocate to the creative and complex aspects of their jobs. Above all, automation will help your workers complete their tasks faster and more precisely. Precisely because of that, RPA plays an immensely important role in manufacturing businesses. Statistics say that RPA was the fastest-growing enterprise software category in 2018. Namely, 53% of businesses interviewed said they already invested in RPA, while in the next two years, this figure will reach 73%.
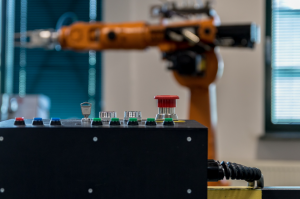
RPA can streamline many aspects of manufacturing, including order processing, regulatory compliance, and transport management. As there are many ways to implement RPA into your manufacturing company, you will first need to carefully reassess your business operations and investigate all potential implementation options. Choose manual tasks prone to error that may cause additional delays and impact your bottom line.
- Train Employees Regularly
For manufacturing businesses, employee training and education is an ongoing process. While some forms of training are obligatory, such as safety training programs, you should also provide additional education opportunities that would help employees stay on top of the latest industry trends and technologies. Apart from training programs focused on machinery, you should also invest in your employees’ soft skills. For example, why not educate your workers about workplace harassment or the benefits of transparency and collaboration?
The major advantage of employee training is improving the overall workplace performance, help employees adopt new industry trends and technologies, and save you lots of time. Apart from increased efficiencies in business processes, training employees is an amazing opportunity to boost their satisfaction and retain them. Research says that 68% of workers believe that employee training is the most significant company policy, while 40% of employees who are not satisfied with training opportunities will leave their job within a year.
- Schedule Maintenance Regularly
Preventive maintenance costs less than the downtime caused by faulty tools. Precisely because of that, equipment maintenance is a fundamental aspect of your process efficiency. For starters, schedule preventive maintenance regularly and keep it consistent. Next, you will need to set clear standards your employees will follow when using and testing equipment. For instance, if your employees notice anything usual about the machine they are using, they should know how to report the problem so you can perform a detailed investigation. The idea is to educate your operators both in everyday maintenance and troubleshooting processes.
Here are a few simple steps to take when injecting consistency into the equipment maintenance process:
- Make a template that will provide detailed explanations of all important steps for maintenance, classified by the type of machinery.
- Choose how often maintenance checks should be performed (daily, weekly, monthly, etc.)
- Create tables where a person who performed the checkup can sign and provide their contact information.
Over to You
Remember that these tactics will not help you achieve overnight success. You will need to adapt them to your specific business’ needs and strategize them thoroughly to maximize your business operations’ efficiency. Additionally, don’t forget to measure their success. Set clear goals and metrics to track and, most importantly, don’t forget to seek employee feedback.
How do you improve manufacturing process efficiency? If you have any additional tips or questions, please let us know!
Join the conversation!