When it comes to ensuring that you implement warehouse best practices, schedule regular reviews of your safety plan to make sure that they remain in line with updated legal requirements, as well as the ever-changing potential risks of your unique work environment.
Your staff are vital to your business running successfully, and providing a safe environment to work in needs to be at the top of your priority list – never mind the fact that it is your legal obligation to do so.
It is far too easy, and unfortunately all too common, for Warehouse managers to let safety procedures slide, especially during particularly busy periods with stressful deadlines. It is essential to remember that maintaining safety standards is imperative to protecting workers, as well as avoiding expensive claims of compensation in the unfortunate event of a work-related accident or injury.
To help ensure the safety of your staff, here is a handy guide as to what must be included when creating a warehouse safety plan.
1. Perform regular safety assessments to identify hazards
Warehouses can be busy places, and each has to manage its own unique set of risks and challenges to navigate. To create an effective safety plan, it is essential to begin by identifying any potential hazards. For example, a cord running along a walkway or a set of steps missing a handrail could both result in someone falling and injuring themselves.
For every identified hazard, consider the measures you can take to either eliminate the danger completely or at least significantly reduce it.
It’s also important to recognize that other potential unforeseeable hazards could arise in the future. As staff move products around the warehouse or when new equipment is being introduced, the potential for new hazards can develop. It’s vital to train and encourage your staff to look out for and report any new dangers that arise in the warehouse.
2. Maintain safe and clear paths
Trips, slips and falls are one of the most common causes of injuries when it comes to warehouse work, so it’s extremely important to maintain clear pathways for forklifts and workers to traverse. Keeping your warehouse clear and clean should be maintained as you go, and anything that requires urgent or specialized attention must be immediately reported.
3. Install safety signage
Marking out safe passageways and clearly labelling any hazardous materials or items is essential to maintaining a safe warehouse environment. They serve as a reminder to staff of the importance of wearing appropriate safety equipment or taking any other appropriate safety action.
Safety signage also helps to inform any visitors of potential dangers while in your warehouse. The safety signage required for each warehouse is dependent upon its unique processes, so it is best to research and order signage related to your warehouse’s particular field and safety protocols.
Additionally, to ensure that your staff adhere to your warehouse’s shelving engineer’s guidelines, it is a legal requirement that signage stipulating safe load amounts are in clear view.
Include a racking audit in your regular safety plan review to ensure that your load signage is up-to-date.
4. Provide safety equipment
There are a number of attachments and accessories that, when correctly used, add further protection for your staff over and above what should already be the careful use of equipment. For example, adding emergency stop systems to any motorized equipment or adding safety guards to machinery or railings to mezzanine floors and stairs.
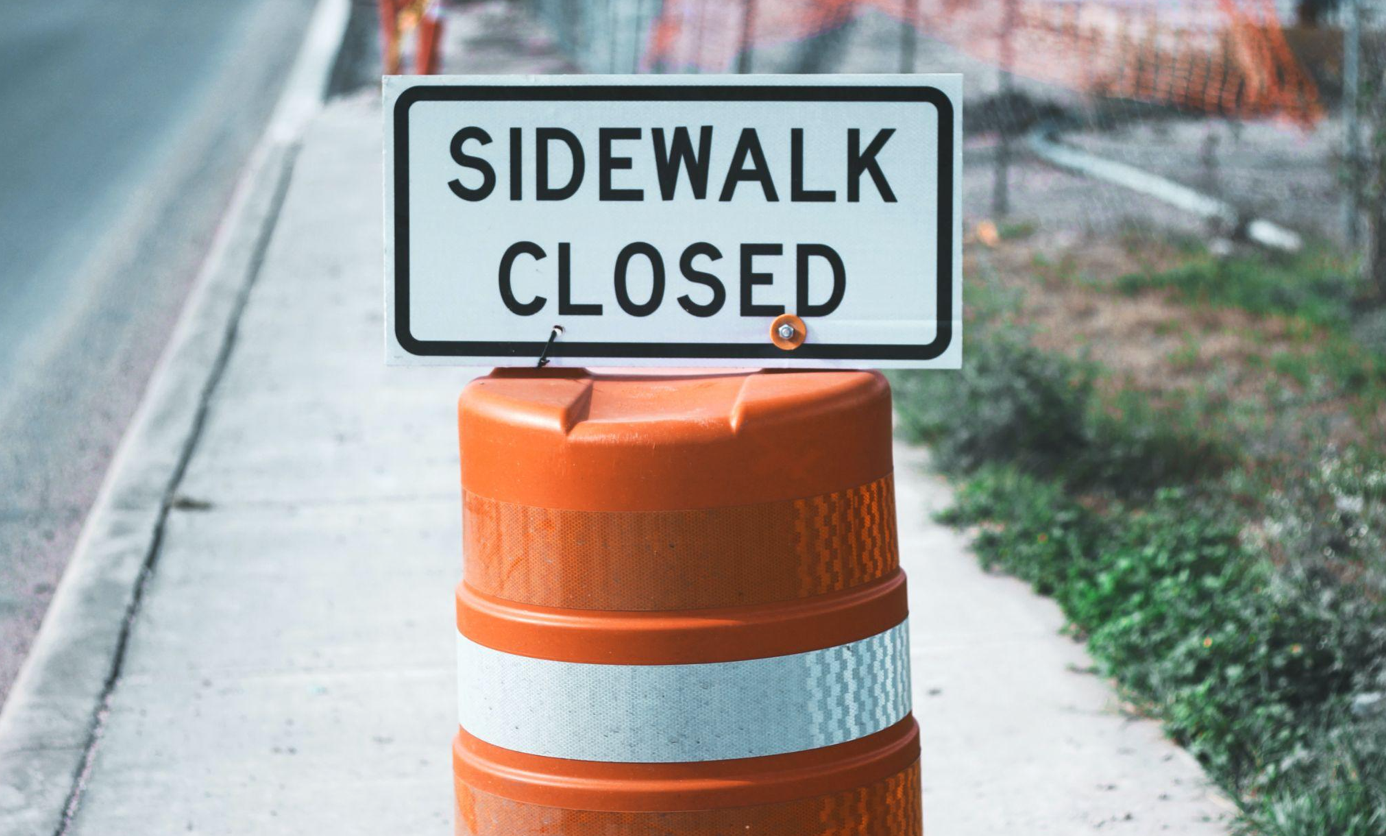
All staff working in a warehouse environment must also wear the necessary safety accessories, to include:
- Protective goggles/eyewear
- Hard hats
- Gloves
- Closed toe/work boots
- Face protection
- High-visibility clothing
- Industrial ear muffs/earplugs
5. Clearly communicate your safety guidelines
When it comes to implementing your safety warehouses procedures, the job isn’t over when you’ve hung up safety signage and implemented a warehouse management plan. It is your legal obligation to ensure that all staff receive the appropriate training in understanding the unique hazards of your warehouse and how best to minimize the associated risks.
To ensure that all warehouse employees are kept aware of all potential risks in their work environment, training must be conducted regularly, to include how staff can act to reduce the risk of causing themselves or others an injury.
Maintaining a high priority attitude towards your staff’s safety also demonstrates that you value them and encourages them to follow your lead.
6. Inspect pallet racking annually
It is a legal requirement that warehouse shelving be inspected every year. Before posing any danger to your employees, a qualified engineer can assess your shelving for any damage large or small and ensure that it is repaired. An annual inspection is also the perfect opportunity to ensure that your load signage is up to code.
7. Conduct regular forklift training
A forklift is generally considered to be one of the most dangerous items of equipment in any warehouse. Incidences of tipping or collisions with workers can cause severe injuries and even fatalities.
It is imperative to ensure that your staff are appropriately and regularly trained on the correct and safe operation of a forklift. It is also a legal requirement to ensure that their forklift licenses are valid to significantly reduce the risks associated with forklifts being operated in your warehouse.
Final thoughts
These are just some of the vital components to include when creating a warehouse safety plan.
When it comes to ensuring that you implement warehouse best practices, schedule regular reviews of your safety plan to make sure that they remain in line with updated legal requirements, as well as the ever-changing potential risks of your unique work environment.
Join the conversation!